Downtime hits every industry hard in costs, productivity, and time. Downtime is when operations come to a standstill, either planned temporarily (scheduled) or unplanned (unexpected).
Scheduled downtime can be helpful. Manufacturers plan downtime in advance to perform repairs, maintenance, or equipment updates. On the other hand, unplanned downtime due to unexpected outages, equipment failures, breakdowns, or supply chain disruptions can be extremely disruptive and costly to the business.
How Costly is Unplanned Downtime for Manufacturers
Unexpected equipment failure or shutdown causes unplanned downtime, an expensive problem for manufacturers. Downtime costs manufacturers approximately $50 Billion annually, according to Plutomen. Pingdom.com estimates that downtime costs manufacturers an average $260K per hour. This equates to 800 hours of downtime annually, encompassing maintenance, tool breaks, and adjustments.
The True Cost of Downtime Report by Siemens unveils insights from a study of 72 major global industrial and manufacturing companies. Large plants lose an average of 323 production hours annually, costing $532,000 per hour. This adds up to $172 million per large plant annually, encompassing lost revenue, financial penalties, idle staff time, and line restart expenses.
The Numbers that Illustrate Downtime Costs:
Unplanned downtime impacts manufacturers differently based on the industry. Let’s look at downtime costs in the following sectors: Automotive, FMCG & CPG, Heavy Industrial, and Oil & Gas.
Automotive Downtime
Automotive plants face the highest unplanned downtime, losing 29 monthly production hours for $1.3 million per hour. FG500 automotive manufacturers estimate yearly losses of $557 billion and 414,800 hours. Notably, 67% prioritize predictive maintenance to avoid losses incurred by unplanned downtime. (Related reading: Minimizing Spindle Downtime: Prevenative Maintenance & More)
Minimizing Spindle Downtime: Preventative Maintenance & More
FMCG & CPG Challenges
FMCG and CPG manufacturers endure 25 monthly downtime hours, costing $23,600 per hour. This totals 1.5 million hours and $35 billion in annual FG500 losses. Impressively, 72% integrate predictive maintenance.
Heavy Industrial Struggles
Heavy industrial sectors, like mining and metals, grapple with 23 monthly downtime hours at $187,500 per hour. Annual losses for FG500 companies in this sector reach $225 billion. Due to these losses, 60% of these companies prioritize predictive maintenance.
Oil and Gas Setbacks
Oil and Gas producers contend with 32 monthly downtime hours at $220,000 per hour, totaling $84 million per facility. Refineries contribute to FG500 losses of $47 billion from 213,000 downtime hours. With 82% prioritizing predictive maintenance, there are efforts to curb unplanned downtime.
Comparison Table of Downtime Costs Across Different Manufacturing Sectors
Here is a table comparing these downtime costs across manufacturing industries:
Industry |
Unplanned Downtime Hours per Facility (Monthly) |
Cost per Hour of Downtime |
Annual Cost per Facility |
Estimated Cost to Fortune Global 500 |
Cost of Downtime as a Percentage of Revenue |
Automotive |
29 |
$1,343,400 |
$468 million |
$557 billion |
20% |
FMCG/CPG |
25 |
$23,600 |
$7 million |
$35 billion |
$220,000 |
Heavy Industry |
23 |
$187,500 |
$52 million |
$225 billion |
$84 million |
Oil and Gas |
32 |
$ 84 million |
$47 billion* |
18% |
1%* |
* Unplanned refinery downtime only: Table based on Isa Interchange article: “
“World’s Largest Manufacturers Lose $1 Trillion/Year to Machine Failure.”
Unplanned Downtime: The Hidden Costs You Should Know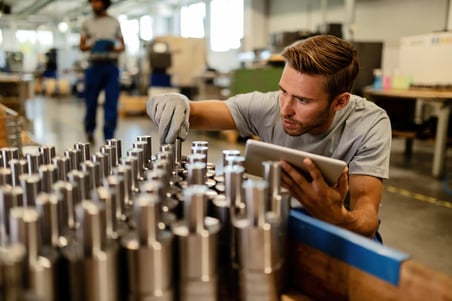
Picture this: the average manufacturer has 800 hours of equipment downtime yearly, roughly 15 hours per week. That's a ton of lost time and comes with huge costs.
For example, when an automotive manufacturer's production line stops, it loses a staggering $22,000 every minute. Overall, unplanned downtime generates $50 billion in expenses for industrial manufacturers annually.
When machines stop churning, whether scheduled or not, they swallow 1% to 10% of available production time. These hours can’t be salvaged, causing significant financial losses. Most losses occur in the following three categories:
- Labor costs include in-house maintenance, overtime, and external contractors.
- Production expenses include wasted materials, reduced capacity, and testing.
- Financial impacts encompass lost revenues and tighter profit margins.
Yet, downtime costs aren't only on the surface level. They also include idled operators, shipping, and lost sales opportunities. Disregarding these costs can harm your budget and bottom line.
So, what is the solution to minimizing these unnecessary expenses?
What to Focus on
- Enhancing equipment reliability and uptime.
- Reducing reactive work and work order backlogs.
- Improving technician efficiency and spare parts availability.
Now that we have a clear idea about the costs, let’s discuss factors contributing to unplanned downtime.
Contributing Factors to Unplanned Downtime:
Equipment Failures
Mechanical breakdowns, component failures, or malfunctions in critical machinery can lead to unplanned downtime. Lack of regular maintenance, wear and tear, or unexpected issues with equipment components are often the sources of this type of unplanned downtime.
Power Outages
Interruptions in power supply, whether due to grid failures, electrical faults, or other unforeseen events, can quickly bring manufacturing operations to a halt. Power outages disrupt the functioning of machinery and equipment, causing unplanned downtime.
Supply Chain Disruptions
Delays in receiving essential parts and materials and other unforeseen supply chain issues can lead to production stoppages. Dependence on a single supplier or vulnerabilities in the supply chain increases the risk of unplanned downtime.
Human Error
Mistakes made by operators, technicians, or other personnel during equipment operation or maintenance procedures can result in unexpected failures. Lack of training, miscommunication, or oversight can contribute to human-induced unplanned downtime.
Environmental Factors
Natural weather conditions, earthquakes, or other environmental disruptions can impact manufacturing facilities. These events may damage equipment, interrupt the power supply, or create unsafe working conditions, leading to unplanned downtime.
Addressing these contributing factors through preventive measures, contingency planning, and continuous improvement initiatives is essential for minimizing the impact of unplanned downtime in manufacturing operations.
So, how can we mitigate unplanned downtime? Let’s dive in:
Scheduling Planned Downtime
Preventive Maintenance
Implementing routine maintenance schedules helps companies identify and address potential issues before they lead to unplanned downtime. This includes regular equipment checks, lubrication, and replacement of worn-out parts.
How it could work in practice:
Implementing routine maintenance for a CNC machining center may involve a monthly checklist that includes inspecting cutting tools for wear, greasing the spindle bearings, and replacing coolant filters. Following this schedule, the machine’s performance is consistently optimized, which reduces the risk of unexpected breakdowns and unplanned downtime.
Scheduled Inspections and Upgrades
Planning regular inspections and upgrades during periods of low production demand involves assessing equipment health and implementing necessary updates, enhancements, or technology upgrades to prolong its life span.
How it could work in practice:
A manufacturing facility that produces packaging machinery schedules yearly inspections during a seasonal slowdown. During these inspections, engineers could assess the condition of conveyor belts, inspect electrical components, and implement necessary upgrades, such as integrating new safety features or adopting more energy-efficient motors.
Mitigating Unplanned Downtime:
Predictive Maintenance
Predictive maintenance technologies like sensors and data analytics help forecast equipment failures. This involves monitoring performance metrics and using predictive algorithms to schedule maintenance based on usage and wear.
How it could work in practice
In a power generation plant, sensors are installed on critical turbines to monitor temperature, vibration, and other performance metrics. Predictive algorithms analyze the data to predict potential failures.
When early signs of wear or malfunctions are detected, maintenance teams are alerted to schedule timely interventions, preventing unexpected turbine breakdowns and minimizing downtime.
Contingency Plans
Developing comprehensive contingency plans involves identifying potential risks and outlining step-by-step responses to minimize the impact of disruptions. This includes having backup equipment, alternative suppliers, and emergency response protocols.
How it could work in practice:
A manufacturing facility that relies on a specific raw material for production develops a contingency plan in case of supply chain disruptions.
This plan includes maintaining relationships with alternative suppliers, securing a backup inventory of the critical material, and having a clear protocol for quickly shifting production to use alternative materials if the primary source faces unexpected challenges.
Efficient Changeovers
Streamlining changeover processes for different product runs involves optimizing procedures, investing in quick-change technology, and training staff to expedite the transition, reducing the time needed for equipment adjustments and setup.
How it could work in practice:
A pharmaceutical manufacturing facility employs a lean approach to changeovers in its packaging line. By using standardized formats for packaging materials and implementing color-coded changeover procedures, the production team can quickly switch from producing one medication to another.
Staff members receive specialized training to execute changeovers seamlessly, and modular packaging equipment allows for rapid adjustments. This efficiency ensures minimal downtime between different drug production cycles and maintains the overall operational flow of the facility.
Optimized Production Planning
Employing efficient production planning strategies, such as adopting just-in-time manufacturing principles, minimizes the need for frequent shutdowns and changeovers. This ensures a smooth and continuous production flow.
How it could work in practice:
A car manufacturing plant adopts just-in-time manufacturing principles to optimize production planning. By closely collaborating with suppliers and receiving components coordinated with production needs, the plant reduces the need for excess inventory.
This lean approach minimizes the risk of frequent shutdowns and changeovers, ensuring a continuous production flow aligned with customer demand.
Employee Training
Training staff to identify and address issues promptly fosters a proactive culture that focuses on preventing unplanned downtime through vigilant monitoring. It includes ongoing training on equipment operation, troubleshooting, and emergency response.
How it could work in practice:
Operators and maintenance personnel undergo regular training sessions in an industrial setting to recognize abnormal equipment behavior.
This proactive approach enables them to identify and address potential issues before they escalate. Additionally, employees are trained in emergency response procedures, ensuring a swift reaction to unforeseen events.
Real-Time Monitoring
Implementing real-time monitoring systems involves continuously tracking equipment performance using sensors and connected devices. This allows immediate intervention upon detecting anomalies, preventing issues from escalating into major problems.
How it could work in practice:
In an oil and gas refinery, real-time monitoring is crucial for ensuring the integrity of critical equipment such as pumps, compressors, and pipelines. Sensors are strategically placed to measure pressure, temperature, and vibration.
The real-time monitoring system continuously analyzes this data to detect anomalies that may indicate potential equipment failures. If unusual patterns are identified, immediate alerts are sent to the maintenance team.
This proactive approach allows for prompt intervention, preventing costly breakdowns, ensuring safety compliance, and minimizing the risk of unplanned downtime in the oil and gas production process.
Supply Chain Resilience
Strengthening supply chains by diversifying sources involves collaborating with multiple suppliers and maintaining adequate inventory levels. This strategy reduces the risk of unplanned downtime due to material shortages or disruptions in the supply chain.
How it could work in practice:
An electronics manufacturer strengthens its supply chain resilience by diversifying sources for critical components. By collaborating with multiple suppliers and maintaining strategic buffer stocks, the company minimizes the impact of disruptions in the supply chain, such as transport delays or sudden shortages of essential materials.
Rapid Response Protocols
Establishing efficient protocols for addressing unexpected failures includes having a well-defined escalation process, readily available spare parts, and a skilled response team. This ensures rapid response times and minimizes the duration of unplanned downtime.
How it could work in practice:
An automotive assembly plant establishes rapid response protocols for equipment failures on the production line. These protocols include a well-defined escalation process, a designated team for immediate response, and a stockpile of commonly needed spare parts. This ensures that unexpected failures are addressed swiftly to minimize production interruptions.
Data-Driven Decision-Making
Leveraging data analytics for decision-making involves collecting and analyzing production data to identify patterns, optimize processes, and make informed choices. This proactive approach reduces planned and unplanned downtime through continuous improvement initiatives.
How it could work in practice:
A chemical manufacturing plant leverages data analytics to monitor the performance of critical reactors. By collecting and analyzing production data, the plant identifies patterns that may indicate impending equipment failures.
This data-driven approach allows for proactive decision-making, reducing planned and unplanned downtime through targeted maintenance and process optimization.
Digital Transformation: A Solution for Today and Tomorrow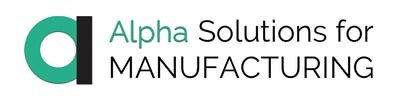
Digital transformation emerges as a solution, particularly in today’s competitive market. This involves integrating digital technology into all operations and promoting a culture shift towards innovation and efficiency.
Connected worker platforms are digital tools that minimize downtime incidents and associated costs. Technicians use mobile devices like smartphones and tablets to perform tasks and share real-time information, enabling swift decision-making.
These platforms cater to planning, inspections, and inventory management, providing actionable insights into productivity and downtime.
While connected worker platforms offer tremendous benefits, alternatives like mobile frontline worker applications or in-house systems exist. However, compatibility issues and information silos might pose challenges in these alternatives.
How Mobile Technology and Low-Code Platforms Provide an Easy Route to Digitalization?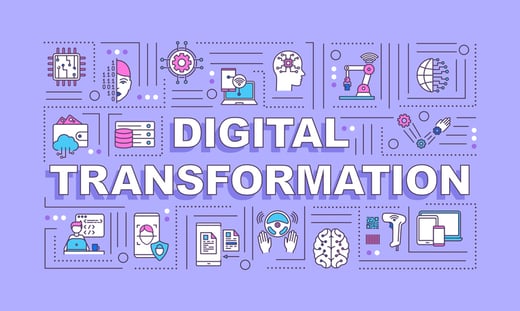
Make Inspections More Efficient
Mobile technology is driving digitalization in manufacturing. Low-code and no-code platforms help manufacturers build solutions to monitor equipment and help with inspections, such as Alpha Software’s Gemba Walk app, enabling quick and accurate data collection, access, and sharing across an organization.
>>Recommended Reading: How Intelligent Apps Can Aid Trailer Manufacturers<<
The best thing is that low-code and no-code platforms need minimal technical expertise. It reduces IT backlog, with developers managing more technical app customization and security. Mobile apps empower workers on the factory floor, allowing real-time data collection and rapid analysis.
Replace Paper Forms with Mobile Digital Forms.
Replacing paper forms with mobile apps improves efficiency, offering instant, accurate data, enabling faster analysis, improving worker productivity, and supporting knowledge sharing.
Small and medium-sized companies can digitize operations using accessible low-code/no-code software, enabling custom app creation without coding. This digitization is crucial for modernizing manufacturing practices across all manufacturers, large and small.
>>Recommended Reading: Digital Transformation Is Tough, But Worth It<<
Bottom Line
Minimizing unplanned downtime through proactive maintenance and digital transformation is crucial for modern manufacturing’s efficiency and longevity. Implementing predictive maintenance strategies minimizes disruptions, ensuring increased productivity and cost savings.
Integrating mobile technology and low-code platforms streamlines operations and enhances data collection while fostering data-driven decision-making. Embracing these digital tools empowers manufacturers of all sizes to adapt, innovate, and remain competitive in an evolving industry landscape.
Comment