Learn how to eliminate risk when changing material suppliers.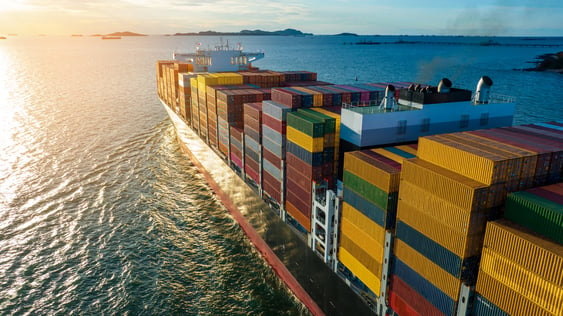
Manufacturers must often change suppliers in a constantly evolving market to stay competitive, but making the change can feel overwhelming. In this blog, you'll discover five seamless strategies for transitioning suppliers, reducing stress, and simplifying the process. These steps will secure a new supplier that aligns with your needs without disrupting production.
Are you considering shaking up your supplier lineup? Dive in!
You've been contemplating the potential benefits of tweaking your supply chain for some time now.
Here are five key reasons to consider changing your supplier:
- Inability to manage costs effectively.
- Deteriorating quality control
- Lack of a specialized team catering to your needs
- Need for more infrastructure to scale up production.
- Poor communication and transparency
While other factors might be at play, these are among the most common ones we’ve seen as we've worked with manufacturers.
Regardless of your motive, there are five steps to make the right changes.
1. What Are Your Needs?
Begin by assessing your needs to get a clear picture. Involve your team in evaluating your current supplier, considering their strengths and weaknesses.
Make a detailed list of your requirements, considering past solutions might not fit your current needs.
The core question is whether your supplier can support your future growth while increasing product quality.
2. Exploring Options: Your Due Diligence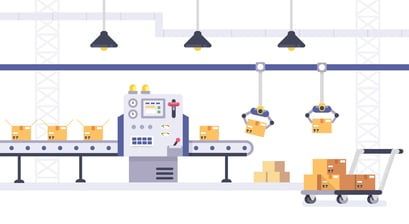
This phase requires dedicated time as you delve into choices—the more pressing the issues, the more precise the need for a new production partner.
Steps to consider:
- Seek supplier recommendations from your network.
- For standard parts, consider less expensive material source suppliers cautiously; otherwise, explore other avenues.
- Transparency is critical when contacting new suppliers; acknowledge that the transition may take time.
- If workable, visit them personally or use third-party audits, especially in distant locations.
- Thoroughly assess potential suppliers, employing a thorough evaluation checklist.
- Reflect and learn from past experiences for a smoother transition.
3. Knowledge Transfer and Data Testing
Now, it's time for you to look at your potential new supplier's capabilities. To do this effectively, provide them with your product data and evaluate their outcomes, typically through a quote.
Request for Quotation (RFQ)
During the RFQ, ensure you provide the supplier with essential details to help them produce a comprehensive quote:
These details may include:
- 2D & 3D Drawings
- Bill of Materials (BOM)
- Functional prototype
- Minimum Order Quantity (MOQ) and annual volume forecast
- Target Price for projected volumes
Quote Reception
Once you receive the RFQ, the new supplier will supply quotes for various aspects, including assembly, raw materials, quality control, packaging, and shipping. Confirm if you're transferring existing tools or setting up new ones to reduce risks.
Sampling Process
Once the quote is accepted, the source supplier's sample production gauges their capability. Multiple defects at this stage could signal a mismatch, prompting a search for an alternative supplier.
Assessment
Having gathered quotes and samples from multiple suppliers, evaluate your situation. Assess whether the received samples and quotes warrant changing your current supplier.
4. The Pre-Production Phase
Upon finding the supplier that fits your needs, the following steps involve transitioning into the production phase:
Finalizing the Agreement:
Confirm the contractual terms and conditions with the chosen supplier. This agreement details business relationships, including responsibilities, timelines, and expectations.
Alignment of Ongoing Tasks:
Ensure any ongoing tasks or developmental activities are consistent with the planned production schedule. Address any pending issues or charges that might set back the production timeline.
Preparation of Tools and Equipment:
Gather and set up the necessary tools, fixtures, and machinery for production. This step ensures that the infrastructure needed for manufacturing or assembling products is set up and operation-ready.
Creation of a Benchmark Sample:
Develop a prototype or sample that reflects the desired production standard. This 'ideal sample' is a reference point for quality control. It should also ensure that later products satisfy these standards.
Establishment of Production Line Guidelines:
Organize the production line by setting up workstations, detailing assembly instructions, and perfecting the workflow. A well-structured production line supports the consistency and flow of the manufacturing process.
5. Launch, Support, and Iterate
After resolving pilot phase challenges, the focus shifts to scaling production to meet demand. Overcoming these hurdles completes the supplier transition, ensuring consistent, efficient production.
Pre-production confirmation leads to the first production phase with a pilot trial. This is essential when changing suppliers but keeping the same product.
A word of caution: expect challenges during this trial. Adapting to change takes time, especially with new personnel, machinery, and tools. A pilot run is crucial for finding and resolving issues before starting full-scale production.
>>Recommended Reading: No-Code Low-Code Can Solve Supply Chain Woes<<
Two Hypothetical Examples of Changing Suppliers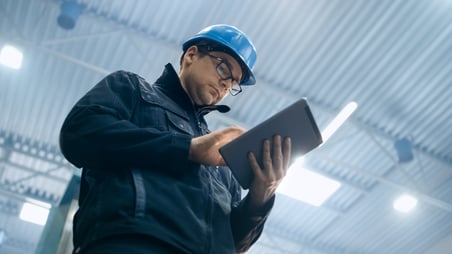
Creating a clear picture helps you visualize what changing suppliers entails. Here are two examples to help you understand the process.
Tech Innovators Inc.
Tech Innovators Inc. specializes in developing innovative software solutions. Due to scalability issues, they changed their current server provider to a new one. After careful evaluation, they select a supplier with better infrastructure and scalability options. The transition involves a pilot phase to evaluate the new server's performance, ensuring it meets its stringent requirements. Once the challenges are overcome, they scale up their server capabilities, ensuring seamless operations for their innovative software products.
AutoTech Motors:
AutoTech Motors focus is on manufacturing electric vehicles (EVs). They've been using a particular battery supplier for their EVs but need help with supply consistency. Looking for a more reliable supplier, they chose a new battery manufacturer renowned for innovative technology and stable production capabilities.
AutoTech conducts a pilot phase during the switch to assess the new batteries' performance, durability, and efficiency. This trial helps show compatibility issues and ensures the batteries meet their EVs' specific power requirements.
Once they successfully navigate the first challenges and ensure compatibility, AutoTech will scale up production with the new battery supplier. This enables them to meet the increasing demand for EVs while providing reliable and efficient battery performance.
While it can be beneficial to change suppliers, risks are also detailed in the section below.
Risks of Changing Suppliers
Changing suppliers can bring various risks and challenges that manufacturers need to address. Some common risks associated with switching suppliers include:
● Supply Chain Disruptions:
Transitioning to a new supplier involves supply risks, especially if the new one misses deadlines or meets quality issues.
● Quality Control Issues:
The new supplier may need to meet the required quality standards, leading to defective products and customer dissatisfaction.
● Financial Stability:
Check the new supplier's financial stability to meet production needs and sustain long-term partnerships.
● Logistical Challenges:
Changing suppliers may require adjustments to planning and transportation arrangements, leading to delays and increased costs.
● Knowledge Transfer:
When knowledge is transferred to a new supplier, it affects how efficiently things are made and their quality. Efficient transfer is critical for supporting production standards during the transition.
Manufacturers must conduct thorough checks on potential new suppliers and communicate clearly with old and new ones for a seamless transition.
Reducing Manufacturing Risks
Manufacturing risks can significantly affect the smooth flow of operations and the overall performance of the supply chain. To mitigate risks, manufacturers should focus on the following strategies:
Supplier Collaboration:
Establishing collaborative relationships with suppliers can enhance communication and enable proactive risk assessment. Regular engagement and information sharing can help identify high risks and develop mitigation strategies.
Use Multiple Suppliers:
Relying on a single supplier increases the risk of disruptions. Manufacturers should consider diversifying their supplier base to reduce dependency and better manage risks.
Continuous Monitoring:
Implementing a robust monitoring system can help show manufacturing risks in real time. This includes monitoring key performance indicators, quality control processes, and supplier compliance.
Contingency Planning:
Developing contingency plans for potential manufacturing disruptions can help minimize the impact on operations. Manufacturers should have alternative suppliers and backup plans to ensure a seamless production flow.
Investing in Technology:
Leveraging technology solutions, such as no-code or low-code platforms, can streamline manufacturing processes and improve the supply chain’s overall efficiency. These platforms enable manufacturers to build solutions with minimal coding knowledge to automate workflows, reduce human error, and enhance data analytics for better risk management. By adopting these strategies, manufacturers can mitigate manufacturing risks and ensure a resilient and efficient supply chain.
Bottom Line
Switching suppliers poses risks like supply chain disruptions and quality issues. Employing no-code or low-code platforms can aid in managing operations and reducing risks when changing suppliers. Diversifying suppliers also helps spread risk. However, thorough assessment, planning, and communication with old and new suppliers are still crucial for a smooth transition while maintaining quality and production continuity.
Comment