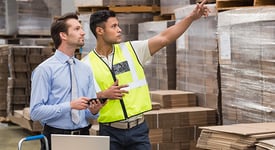
A digital Gemba Walk checklist can be used and customized for any organization. Gemba Walk observations are useful to just about any business in any industry and are becoming more widely used. They involve walking through workplaces and capturing observations on a checklist, which can help companies identify inefficiency, waste, and safety hazards.
What is a Gemba Walk?
To improve operations, leaders must understand the processes behind them, and the daily challenges, physical tasks, and technology the people responsible for those processes use.
When managers in "ivory towers" make decisions without knowing the details, they may make unreasonable requests. At the same time, those doing the work are often too busy or close to the process to address potential problems. When managers take a step back and watch a process happen, improvement opportunities can be seen quite clearly.
A management system that incorporates real-world information can raise employee engagement. This provides particularly valuable insights into production processes on the factory floor or shop floor.
Toyota's process improvement leaders first developed the concept of a "Gemba Walk." The word Gemba is a Japanese word meaning "the real place". It is now a common kaizen event -- or short-duration improvement projects -- across hundreds of companies.
Gemba walks put process leaders at the location where the work or process is performed.. Leaders are expected to watch the process happen, interview people doing the job, take clear notes and make insights. After observing processes and identifying problems, those insights can help guide future improvements or address challenges and safety issues.
Gemba walks can be used in virtually any industry for any process. For example, checkout lines and areas at grocery stores, warehouses, shipping facilities, call centers, and more. The important thing is to observe carefully, ask workers insightful questions and record observations accurately and comprehensively. Gemba walks can help improve standard work routines and make them safer or more efficient.
Who utilizes Gemba Walks?
Leaders and managers across various industries typically use Gemba walks, particularly in sectors focused on continuous improvement, quality control, and operational efficiency. Here’s a look at who commonly participates in Gemba walks:
- Operations Managers often take Gemba walks. They do this to see the production floor and observe workflows. This helps them find areas for improvement. Their goal is to boost productivity and efficiency.
- Executives and Senior Leaders: Leaders from various departments, like manufacturing, quality assurance, and supply chain, use Gemba walks. They connect with frontline employees and learn about operational challenges. This helps align the organization's goals with daily activities.
- Quality Control and Assurance Teams: Quality specialists use Gemba walks to check if processes follow the standards. They look for defects and make sure quality measures are maintained.
- Lean and Six Sigma Practitioners: These professionals work on Lean, Six Sigma, or continuous improvement projects. They use Gemba walks to see processes in action. This helps them find waste, bottlenecks, and areas for improvement. Their goal is to reduce inefficiencies.
- Supervisors and Team Leads: These leaders take Gemba walks to connect with their teams. They offer support and solve problems that may affect productivity or morale.
- Human Resources and Safety Officers: Sometimes, HR and safety officers join Gemba walks. They address employees' workplace concerns, observe working conditions, and ensure employees are following safety rules.
- Cross-Functional Teams: When a project includes different departments, cross-functional teams can do Gemba walks. These walks encourage understanding of each department's work, promoting better teamwork.
- Consultants and auditors may do Gemba walks during assessments or audits. This helps them see processes up close. They want to make sure operations follow best practices and meet compliance standards.
By doing Gemba walks, leaders and teams gain important insights while the organization fosters a culture of continuous improvement. Faster decision-making and operational excellence are often key outcomes of practicing Gemba Walks.
How do you use Gemba Walks?
A checklist should be used each time a process manager conducts a Gemba walk. This ensures that the process is focused, important items are not missed, and similar questions allow you to better compare answers and progress over time. The checklist should include questions that will help you understand the process better. Your questions will also change depending on the main objective -- or changing objectives -- during your walk.
What types of questions are asked during Gemba Walks?
Some questions typically included on Gemba Walks include:
- Is there an established process for this specific work?
- Do you have any problems with the current process?
- Why is there a problem?
- Can you identify the root of the problem?
- Can you fix the problem?
- Who do you voice concerns or problems with the process to?
- Is there an aspect of your process/job that takes up too much time or wastes time?
These questions will defer when exploring different areas such as: problem-solving, innovation, resources, tools and etc. So before you go Gemba, prepare your checklist carefully based on the area you want to investigate.
What are the benefits of a Gemba Walk?
Conducting regular Gemba walks, resolving issues, and measuring impact can result in:
- Faster identification of unsafe work environments or needed repairs
- Throughput improvements and less time spent by those involved "waiting around" for things to happen
- Reduced waste from operations
- Stronger relationships and common understanding between workers and management
- Continuous improvement of the process and overall operations of the business.
How can I collect my Gemba Walk notes, interviews, and pictures?
In the past, insights from Gemba walks were written on paper. This made it hard to share and measure the data quickly and clearly. With mobile forms, lean manufacturing managers can collect Gemba Walk checklist data on any device. They can easily share this information within the company. (Further reading: Lean six sigma manufacturing software.)
Paperless Gemba walk checklists can make improvements easier. They capture more accurate data and include detailed images and explanations. This is something paper checklists cannot do. For example, a Gemba walk may uncover that a machine on the manufacturing production line is always down. The insight may be that the machine is particularly old and not running efficiently. The improvement may be a new machine, an update, or a critical repair.
By taking good notes during the Gemba walk, managers can accurately record detailed information, pictures, measurements and interview comments. Best practices now involve recording all aspects of the walk digitally. More and more companies are moving paper processes to a mobile app, such as this Gemba app.
Why are Gemba Walks using mobile devices so important?
Using mobile devices for Gemba walks adds a lot of value because they make it easy to capture and share real-time insights, data, and documentation, streamlining the entire process. Here are a few reasons why mobile Gemba walks are particularly effective:
- Real-Time Documentation: Mobile devices make it easy to take notes, capture photos and videos, and enter data. This helps document issues, observations, and improvements right on-site. This immediacy enhances accuracy because insights get recorded on the spot instead of relying on memory.
- You can quickly access information with a mobile device. It allows you to view important documents, past reports, checklists, and other resources directly. This makes it easier to reference prior data, identify trends, and ensure that observations align with company standards.
- Better Communication: Mobile devices facilitate immediate communication with off-site team members, who can provide input in real time. This collaboration can help solve issues faster and get broader input when needed.
- Enhanced Tracking and Follow-Up: Mobile apps for Gemba walks often come with tools to assign follow-up tasks, set reminders, and track progress. This helps make sure that actions from Gemba walks are completed. It also lets team leaders check the status of improvements directly.
- Data Centralization: A mobile app can store data from multiple Gemba walks centrally. This centralization gives insights into ongoing issues and improvements in processes over time. It also highlights common challenges across locations, which aids in decision-making.
- Less Paperwork: Digital documents on mobile devices remove the need for paper. This reduces the chance of losing notes. It also makes it easier to store and find past records. This also supports sustainability efforts by reducing paper use.
Using mobile devices makes Gemba walks more organized and effective, leading to rapid problem-solving and ongoing improvements.
What do I do after a Gemba Walk?
With the right data collection tool, you can share your data and notes, or even add your insights. You can brief teams on what you uncovered. The best lean practices capture and compare each week's Gemba Walk results -- showing continuous improvement over time. Transparency is key.
Free Gemba Walk Checklist App - Available Now
What should you include on your Gemba Walk checklist? We've assembled the list and put it into a mobile app you can begin using immediately. The Gemba Walk Template free download from Alpha Software helps companies collect and share critical insights found on routine Gemba walks.
This app allows you to easily share insights with your colleagues through an Excel file or tie it into your systems of record. The app can be reused to accommodate your company's Gemba walks schedule.
Business leaders can take pictures, record notes, time and date stamp their walkthroughs, interview team members, and more. Alpha Software offers a range of quality manufacturing solutions. Learn more about quality control and quality assurance apps.
Let us help you with identifying areas for improvement at your organization.
Book a meeting with us and get free access to the Gemba Walk Solution.
Free Access to the Alpha TransForm Gemba Walk App
Key features of Alpha TransForm's Gemba Walk App include:
This manufacturing app is a robust solution for organizations aiming to enhance their Gemba Walks through digital transformation. By leveraging this app, teams can streamline data collection, improve accuracy, and facilitate real-time analysis, thereby supporting continuous improvement initiatives. |
Comment