Software solutions let you reap benefits from the Data Value Chain by improving all its four links: collection, publications, uptake, and impact.
Data by itself won’t do much for your business. No matter how much data you collect, unless you’re able to analyze it, reap it for insights, and then take action on those insights to help your bottom line, it has little or no value.
Because of that, there’s been an increasing focus on what’s called the Data Value Chain. What is the chain? The Open Data Watch article “The Data Value Chain: Moving from Production to Impact” describes it this way: “The data value chain describes the evolution of data from collection to analysis, dissemination, and the final impact of data on decision making.”
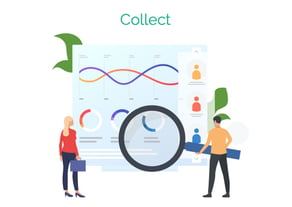
What is the Data Value Chain?
The chain is made up of four phases: collection, publication, uptake and impact.
The collection phase identifies the data to be collected, and then creates a process to collect it. The article adds, “The last phase of data collection involves processing data to ensure they are correctly recorded, classified, and stored in formats that allow further use.”
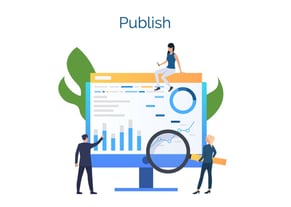
The publication phase focuses on publishing the data and associated metadata so it can be accessed and analyzed. The article says, “As data move through the steps of the publication stage, they increase in value. To optimize their value, it is important to strategically and carefully think through how data will be analyzed, released, and disseminated to encourage use for future impact.”
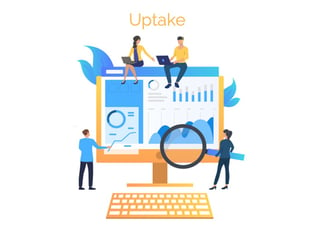
In the uptake phase data is spread throughout a business. This stage, the article says, is made up of three steps: “Connecting data to users; incentivizing users to incorporate data into the decision-making process; and influencing them to value data. Connections to users can be made in many ways: through press releases and online dissemination; by holding trainings, seminars or other educational events; and by improving the user experience offered by websites, data portals, and archives.”
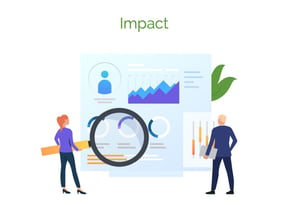
In the impact phase the data is used to make an impact on a business, for the better. The article explains, “The impact stage involves three activities: using the data to understand a problem or make a decision; changing the outcome of a project or improving a situation; and reusing the data by combining them with other data and sharing them freely.”
How to Leverage Digital Technology for Collecting, Analyzing, and Acting on Data
Analyzing data effectively is critical for quality improvement and continuous improvement across manufacturing organizations. Manufacturers often store data in several places, which presents an obstacle to analyzing that information efficiently.
Many manufacturing companies still use cumbersome manual procedures or paper forms. When manufacturing companies do use software, workers are often tied to desktops or dummy terminals around the manufacturing floor. In turn, quality managers spend a lot of their day tracking down missing information or correcting incorrectly keyed data. These older technologies also do not allow workers to collect rich, modern data, like bar codes, pictures, audio interviews, and more.
Tablets and smartphones now exist on many manufacturing shop floors that were once only the domain of desktops and terminals. Inspectors and quality managers are no longer tied down to this hardware and are not forced to take written notes or rely on their memories and then rekey information. Low-code manufacturing management software allows shop floor workers to create custom mobile apps that can record critical manufacturing data - right where it lives. This allows workers to handle material, product quality, and inventory issues at the source. And they can solve and foresee problems faster.
Better, faster collection, analysis, and dissemination of accurate manufacturing data can be an enormous competitive advantage for your organization. This is particularly critical in a competitive market with regulations or supply and price volatility.
The Right Manufacturing Software Solutions for Improving Your Data Value Chain
So how can you do all this? You need the right software partner to help you build apps for collecting, disseminating, analyzing, and ultimately making use of data.
Alpha Software is a trusted solution supplier to major manufacturers, including Boeing, Fenner-Dunlop, and Nestle-Purina,
Alpha Software Manufacturing Solutions can improve every link in the Value Data Chain:
- Collection - Employees can collect more manufacturing data faster when they use mobile apps built with Alpha Software (automate time/date stamping, take pictures, scan bar codes, etc.).
- Publication - With Alpha Software apps, digital information can be shared and analyzed anywhere, instantly in a range of formats (analytics, reports, dashboards, emails/SMS alerts).
- Uptake - Manufacturing apps built with Alpha Software can tie data into systems of record, workflows, daily routines, and processes.
- Impact - Alpha Software manufacturing solutions allow you to take action on the data (immediately take steps to avoid supply shortages, repair a broken machine, kickoff a non-conformance report, etc.).
Alpha Software builds powerful manufacturing apps for your quality teams, turning any paper form into a mobile data collection app with built-in analytics. A built-in analytics engine allows managers to visualize all their data from these apps, and share reports and dashboards, integrate data with existing databases, or trigger workflows.
Contact us to discuss your needs - we'll build the right solution for you.
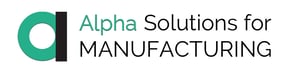
Powerful Manufacturing Apps for Inspectors, Engineers, Assemblers, and Production Teams
Gemba Walks • Workplace Audits • Non-Conformance Reports • Yellow Sheets • 5s Audits
Temporary Deviation Authorizations • Shortage Sheets • Supplier Defects Per Unit Reporting • ISO Certification
Workplace Wellness • Work in Progress Tracking • Inventory Management • Quality Management • and more,,,
Comment