5S audit checklists and 5s audit apps provide an excellent way to make continuous improvements in any organization. Read about 5S Audits and get free access to a digital 5S audit solution with a built-in 5s daily audit checklist.
While traditionally done on paper, 5s audits are more comprehensive, timely, shareable, and searchable when completed on mobile devices. Digital 5S audit apps collect data more accurately, capture images and rich data, and streamline improvements in ways paper forms.
Lean Manufacturing
Lean manufacturing is a methodology that is widely used to optimize production processes and reduce waste. The lean business methodology promotes a flow of value to the customer using two key focuses: continuous improvement and respect. Jim Benson of Modus Cooperandi explains:
“Lean is both a philosophy and a discipline which, at its core, increases access to information to ensure responsible decision making in the service of creating customer value.”
While it is commonly associated with the manufacturing industry, the lean methodology can be applied to other industries such as construction, healthcare, hospitality, and retail. Manufacturers have created over 25 lean tools to help apply the lean methodology to their business in a way they can record and measure. Let's take a look at 5 popular lean tools.
Lean Tools for Manufacturing
By applying lean manufacturing methodology to a business can help companies stay competitive in a rapidly changing business environment. Some key lean tools used to improve operational efficiency include 5S, kaizen, gemba, kanban, heijunka, and poka-yoke. By using these tools in combination, companies can create a culture of continuous improvement and achieve significant gains in efficiency, quality, and customer satisfaction.
- 5S involves organizing workspaces to make them more efficient, effective, and safe.
- Kaizen, for example, is a continuous improvement process that involves making small, incremental changes to processes and procedures.
- Gemba is a Japanese term that refers to the place where work is done, and the gemba walk is a method of observing processes in action to identify areas for improvement.
- Kanban is a visual management tool that helps teams manage workflow and inventory.
- Heijunka is a method for smoothing out production processes to minimize fluctuations in demand.
- Finally, poka-yoke is a quality control technique that involves designing processes and products in a way that prevents errors from occurring.
By using these tools, companies can create a culture of continuous improvement. They can achieve significant gains in efficiency, quality, and customer satisfaction. Whether in manufacturing or other industries, the principles of lean can help companies stay competitive in a rapidly changing business environment.
Let's focus more closely on one of the foundational aspects of lean manufacturing, 5S.
5S Audits
As previously stated, 5S organizes workspaces to achieve higher levels of safety and efficiency. By organizing tools, materials, and equipment using the 5S methodology, companies can minimize wasted time and effort, thereby increasing productivity and reducing costs. A clean, organized facility increases the likelihood that production will run smoothly. 5S Principles - which often take the shape of a "5S Audit" -- assess workspaces to ensure maximum efficiency, worker safety, and unnecessary waste.
This 5S system, which began as a manufacturing method used by Toyota, focuses on putting everything in its proper place and keeping workspaces clean. The term "5S" comes from five Japanese words that represent a 5-step process for organizing spaces so work can be performed efficiently, effectively, and safely:
- Sort (Japanese: Seiri
- Set in Order (Japanese: Seiton)
- Shine (Japanese: Seiso)
- Standardize (Japanese: Seiketsu)
- Sustain (Japanese: Shitsuke)
5S Audits - which tape the shape of 5s checklists -- assess workspaces to ensure maximum efficiency, worker safety, and unnecessary waste.
Benefits of 5S Audits for Manufacturing
5S audits improve the overall function of a business by making it easier for people to work efficiently and safely by eliminating waste and on-the-job injury. Companies that regularly conduct 5S Audits using a routine checklist see continuous improvement.
Specific benefits of 5S Audits performed as a daily routine include:
- increased productivity
- lower costs
- improved quality control and quality assurance
- increased worker safety
- higher worker satisfaction
- measured progress.
Historically, managers conduct 5S audits using paper and clipboards. But continuous improvements can accelerate when managers use mobile apps (or digital forms) to conduct 5S audits.
Paper 5S Audits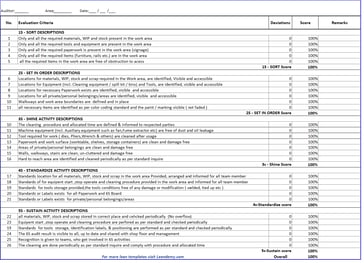
To conduct a 5S audit using paper and clipboard, managers typically use a 5S checklist template that outlines the five steps of the 5S methodology: Sort, Set in Order, Shine, Standardize, and Sustain. They walk through the workspace, observing and noting the condition of the area and the level of adherence to each step of the methodology.
This process involves manually checking off each item on the paper checklist and recording any notes or comments. The checklist may include questions such as, "Are all tools and equipment in their designated place?" or "Is the workspace free of clutter and debris?"
Once the audit is complete, the manager may compile the data and analyze it to identify areas that need improvement. (Leandemy offers an example of a 5S audit checklist excel template (see image).)
While paper and clipboard audits can be effective, they are time-consuming and laborious, and the data collected can be challenging to analyze and track. Digital 5S audit apps provide a more streamlined and efficient way to conduct audits and collect and analyze data in real-time.
Digital 5S Audits
In the past, managers would conduct 5S audits using paper and clipboards, which was a time-consuming and laborious process. It was also difficult to analyze and track the data collected, making it challenging to identify areas that needed improvement. However, with the advent of technology, digital 5S audit apps have revolutionized the way audits are conducted. These apps provide a more streamlined and efficient way to collect, analyze, and monitor data in real-time, making it easier for organizations to achieve their goals and continuously improve their processes.
When you turn a paper 5S audit checklist into a digital 5S audit app, manufacturing leaders can collect data, analyze data, and monitor progress faster.
Digital 5S audits have the potential to collect a greater amount of data than what can be collected on a paper form. This is because digital audits can easily capture images and videos, record audio, and automatically timestamp each entry. Moreover, digital audits can be programmed with skip logic, which means that they will only display relevant questions based on previous responses, making the audit process more efficient. With digital audits, companies can also set up custom notifications and alerts to remind team members of their responsibilities and deadlines. All these features combine to make digital 5S audits a powerful tool for continuous improvement in any organization.
Digital 5S audit apps not only allow for faster data collection and analysis, but they also provide real-time monitoring of progress. This means that manufacturing leaders can quickly identify areas that need improvement and make necessary changes to optimize their operations. With the ability to access data on the go, managers can make informed decisions and take immediate action to address any issues. Additionally, digital 5S audit apps often come equipped with features such as automated notifications and reminders, making it easier for teams to stay on top of their audits and ensure that they are completing them thoroughly and accurately. Ultimately, digital 5S audit apps provide a streamlined and efficient way for organizations to continuously improve their processes and achieve their goals.
Once you decide to use a digital checklist, there are important questions to answer, including:
- How do you plan to capture the audit data (smartphones or tablets) and ensure a complete assessment is done correctly?
- Can you view the collected data using visual analytics? Does the solution have pre-built dashboards or do you need to build them?
- How can you share the audit checklist with important team members responsible for inventory, cleaning, equipment repair, or employee safety?
- Where will you store the data? How will you measure improvements over time?
Not only will you want a digital checklist, but you'll want a solution that includes data visualization, data storage, reporting, and more. Not all 5S audit forms are the same.
The Best 5S Audit App - Includes Digital 5S Checklist
Alpha Software has digitized 5s audits and packaged the process in a complete solution for managers.
The Alpha TransForm 5S Audit Solution helps companies begin a systematic approach for 5S Audits, including fast capture, sharing, and reporting of the data associated with these audits. Companies that use this pre-built 5S checklist template on their mobile devices will speed audits. In turn, teams can improve productivity, cut down on time and inventory waste, and decrease the risk of employee injuries, all while tracking continuous improvement.
The 5S audit solution is one app the Alpha TransForm Quality Management Solution for quality teams. In addition, the Company offers a host of lean manufacturing apps and templates for manufacturers.
Contact Us for Free Access to this Solution Today
In 10 minutes we can provide access to the 5S Audit Solution and several others and help you customize them for your needs - for free!
Further reading on lean manufacturing and how mobile apps can deliver continuous improvement:
Read more about the quality management software from Alpha Software.
- Benefits of using low-code apps in lean manufacturing
- Examples of low-code apps powering continuous improvement
- Learn about quality management software from Alpha Software.
Comment